
AC40 foiling monohull
The AC40 foiling monohull, an ETNZ and McConaghy collaboration
A long-distance collaboration between Emirates Team New Zealand (ETNZ) and McConaghy boatbuilders in China to produce the new AC40 class of foiling monohulls resulted in both parties lifting their game to achieve an exceptional result.
ETNZ undertook the design of the new machine, which packs a host of complex hydraulic, mechatronic and electronic systems within its 11.8m length, but had to find a build partner with the highest possible composite credentials and the capacity to do a production run within a very tight timeframe.
Founded in Sydney in 1967, McConaghy has produced some of the world’s most successful maxi yachts, including Alfa Romeo and seven-time Sydney-Hobart winner Wild Oats XI, along with high-tech defence and aerospace commissions and a deep-sea submarine for movie-maker James Cameron. In 2006, the company expanded into China where it operates from a high-tech 20,000m² facility.
‘This project was definitely a step up to the next level for us,’ says group director Mark Evans. ‘It is a small package, but the level of composite engineering and internal systems is highly complex.’
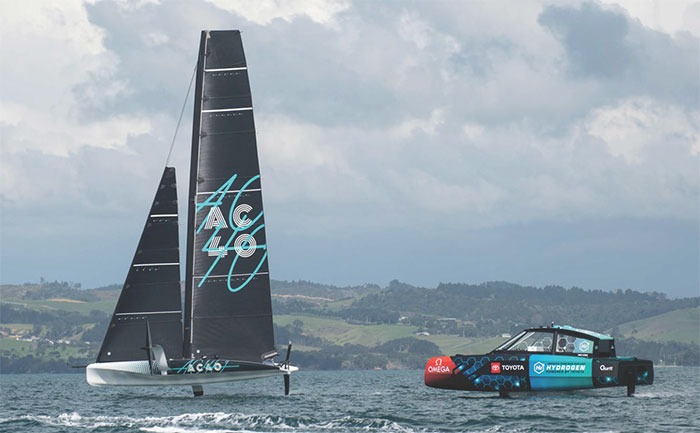
In the first instance, the AC40 will be used by all the America’s Cup teams as a training and development tool as well as competing in various World Series regattas in the run-up to the 2024 regatta in Barcelona. Out of competition, AC teams can test experimental foils and sails, but in competition strict one-design rules will apply.
In addition, the AC40 fleet will be used for the Youth and Women’s America’s Cup events during the Barcelona regatta.
There are also moves afoot to open the class to private owners to set up a unique foiling monohull race circuit independent of the America’s Cup. This would put owner-drivers in the hot seat of scaled down America’s Cup yachts sporting the most up to date foiling technology capable of more than 40 knots.
‘We are already talking to a number of prospective owners,’ says Evans. ‘We are identifying potential regatta locations in Europe and putting together documentation on how the class would be managed with technical support from ETNZ and McConaghy.’
With the level of interest already high, Evans says the owner-driver class could be established before the end of 2023.
The boat is delivered ex-factory complete with all systems installed, batteries, charging system, cradle, flat rack transporter, Southern Spars mast and rigging, North Sails wardrobe and on-board instrumentation system. ‘The price of the boat would be very competitive against a high-spec TP52 SuperSeries yacht and with only three professional crew, the campaign costs would be significantly less,’ says Evans.
No holding back
Despite its multipurpose brief, ETNZ design chief Dan Bernasconi says there was no holding back in terms of design. ‘It is a no-holds-barred racing machine. We are putting everything out there with the best foiling 40-footer we could produce in terms of hull shape, foils, sails and control systems.’
The AC40 incorporates the revisions to the AC75 rule following the 2021 regatta in Auckland. These reduce weight, free up the hydraulics specification and widen the wingspan of the main foils, primarily to promote earlier lift-off and improved light-air foiling.
The smooth, flowing lines of the hull reflect hydrodynamic effort to promote early lift-off, combined with considerable aerodynamic refinement to reduce drag in flight; the package represents a distinct advance on what was on show in the AC75 class of 2021.
In fact, Bernasconi believes it would be pretty competitive against a firstgeneration AC75. ‘I would still put my money on the AC75, purely from the size of the boat, but the AC40 would not be very far behind.’
Obviously, distance between the design and build groups – compounded by a Covid-imposed total shutdown on travel – demanded a very high degree of communication and extreme precision both in the design and construction drawings and the execution.
To produce the hull and deck shell, McConaghy CNC milled a hull and deck plug as a single piece and then took separate female moulds for the hull and deck. ‘To ensure a perfect match, we were working to tolerances of less than 1mm,’ says Evans.
When it came to the composite engineering, it demanded another step up. ‘We have done a lot of maxi yachts and a couple of America’s Cup yachts, but, again, this was next level. The first thing I noticed was the range of core types, including Corecell, Nomex and aluminium honeycomb.

‘The other thing I noticed was how light the carbon plies were. On maxi yachts, the carbon skins are super light. With the AC40 it was like building a dinghy. The entire hull shell is incredibly light. Four guys can pick up this 40ft hull and walk it down the factory.
‘Every single carbon ply is CNC cut and kitted, ready to go into the mould. We have two or three people checking every laminate. We have about 80 people working 12 hours a day, seven days a week on this project to produce one AC40 every five weeks.’
The major challenge came with the internal systems installation. ‘Very few companies in the world could match ETNZ’s expertise in the hydraulics, software and mechatronics that make these yachts foil,’ says Evans.
‘They designed every single wire and hose run, modelled it in the computer and sent it to us. Every bracket for every part and connection was modelled. We were building and gluing in carbon brackets before we even received the components.’
In New Zealand, the ETNZ engineers produced a mock-up of the hydraulic installation with all the components in place. This was replicated in China, before it was broken down into modules and installed.
To ensure perfect alignment of the cam pins and hydraulic pins, a steel jig was CNC milled with all the connection points precisely located. ‘The CNC-milled bulkheads are pinned to the jig which is craned into the hull and, with everything 100 per cent aligned, we glue and vacuumbag the bulkheads in place. Then, we release the pins and lift the jig out. That ensures absolute repeatable accuracy.’
Communication between the yard and the design group was virtual, with regular zoom meetings and phone calls, while management of the hundreds of drawings was through Smartsheet software. ‘Every time a new drawing is loaded, the system automatically updates, so you know exactly where you are,’ says Evans. ‘The system allows you to make notes, or ask questions back and forth. It is a system we have used for some time and ETNZ agreed to adopt it.

‘The documentation was exhaustive – the manual for bleeding the hydraulic system alone ran to 30 pages – but the technology makes the management of drawings and amendments quite straightforward.”
From ETNZ’s standpoint, where the primary focus is on one-off custom yachts, designing a production boat added a new dimension, which Bernasconi says will help in developing their AC75 for 2024.
‘Our in-house build team expects reasonably detailed drawings from us anyway, so we have developed good internal processes and very clear communication between the design team and our own build team,” he says.
‘With the AC40, the biggest change was with the hydraulics and electronics. Usually the installation is done with the boat in front of us – obviously with a lot of design beforehand, but not down the level of detail that we had to apply for a boat being built remotely. By the AC40 forcing us to get that much more detailed in our design drawings, we see where we can make efficiency gains in building our own boats.’
Through delivery and commissioning of the first boat off the production line, ETNZ has been hugely impressed by the product and the process. After being subjected to rigorous on-shore load tests and dry-sail systems checks, followed by tow-tests to check the foiling system, the boat was sailing just three days after delivery.
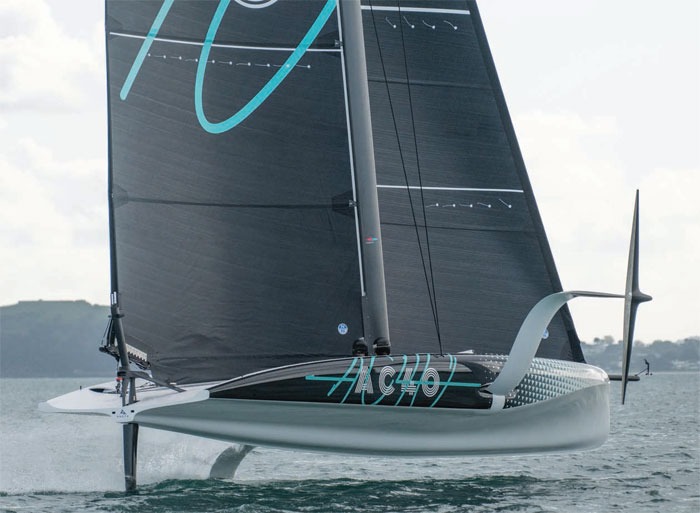
Its first outing was in light to moderate conditions. Within 15 minutes of hoisting the sails for the first time, the AC40 was foiling upwind at 29-31 knots. During that debut session it executed five foiling tacks, 11 foiling gybes and reached a top speed of 36 knots. The polars indicate a top speed of 44 knots in 20 knots of true windspeed, with an upwind speed of 39 knots. ‘I don’t think we will breach the 50-knot barrier with this boat, but it might get pretty close,’ says Bernasconi.
‘I was absolutely blown away by the boat’s performance and how everything worked straight out of the box,’ says Ray Davies, who was part of initial on-thewater test crew. ‘We have had no issues with the boat. The sea trials have been completed and she ticked all the boxes. from day one. It is everything we wanted it to be. We are very confident the AC40 will become a class in its own right and will be fit for purpose for the Youth and Women’s America’s Cup contests, as well as for a private owner-driver class.’
‘You do not need to be an elite helmsman to sail this yacht,’ Davies emphasises. ‘You just need three other very good people around you. This has been the vision for this class from the outset. It is really satisfying to see it happening. We can put hand on heart and say it is real.’
With the flight control fully automated – the helmsman can set the height in 100mm increments – and all the other functions including foil deployment, multiple sail trim inputs, mast rotation and rudder rake powered by hydraulics, it is a push-button boat.
That takes nothing away from the excitement, the action or adrenalin rush. Along with the tremendous speed rush, there are plenty of speed-generating inputs to test the sailing skills, tactical intelligence and teamwork of crews, while taking physical size and strength out of the equation.
This makes the AC40 ideal for women and youth teams, for efficient America’s Cup training and testing purposes as well as opening the possibility of an exciting new owner-driver foiling class.