
Anti-chafe solutions from Future Fibres’ dedicated R&D programme
Anti-chafe solutions from Future Fibres’ dedicated R&D programme
A simple fact sets sailing apart from most other technical activities. When afloat and driven by the wind absolutely nothing involved ever stays still
A sailing boat is an object in motion. The boat itself moves, the sails are moving, ropes are running in all directions. Sometimes the movements are small, sometimes they are big. But to some degree, everything is moving – all the time. This obviously has consequences, and one of them is called chafe. World leading manufacturer of composite rigging, Future Fibres, has completed a multi-year research programme on chafe damage characterisation and mitigation, the outcome of which aims to improve the abrasion resistance properties of the materials currently used in modern composite rigging.
In recent years, chafe issues have become substantially more serious, especially in the high-performance sector of the industry. This has happened for several reasons: first of all, there is the increase in standing rigging made from composite materials instead of stainless steel rod rigging. Secondly, the introduction of a new generation of lines for running rigging, especially Dyneema SK99. Lines have become so strong that smaller diameters are sufficient, and also often used uncovered hence leading to even smaller outer diameters. Thirdly, we now have new types of furling systems, drop line systems, high efficiency winches and other modern sail-handling equipment that make everything much faster than before. Finally, general boat size and rig loads have increased.
So, what used to be a moderate consideration, handled with selfmade protection patches or just plain care and maintenance, is now a different beast altogether. Juanjo de la Cuesta, Future Fibres’ R&D manager, explains: ‘Chafe protection is not a new topic to us. It is one of these constantly ongoing research projects as we are permanently open to trying new materials and solutions. From the introduction of Zylon PBO through to the latest carbon rigging innovations, Future Fibres has always developed and incorporated improved protective materials into product upgrades.’
However, a dedicated chafe protection R&D campaign was launched in 2022. As Future Fibres puts it, ‘with the objective of delivering reimagined anti-chafe solutions resulting from the largest materials study and most demanding test campaign to date’.
The project has burned through more than 2,500 man hours and almost 100 test pieces. The experimental phase included over 200 tests with varying designs and conditions. ‘It is worth introducing that chafe can actually be divided into two regimes: high speed and low speed’ says de la Cuesta. ‘Within these, materials behave differently, and therefore different solutions are needed for different areas of the rigging’.
According to Seth Cooley, chief engineer at Future Fibres, ‘high speed chafe comes mainly from winch-driven spinnaker drop lines running over the headstay during douses, or sheets hauled around vertical shrouds. This is an aggressive, sudden event, involving high speed and tension, and creating high surface temperatures that can ultimately compromise the rigging materials. Low speed chafe, on the other hand, is mostly seen when sailing wide open angles, where for example the eased-out mainsail battens touch the shrouds and spreaders. It takes much longer to create damage, but especially the batten sections can be hard on the shrouds. The mainsail is moving constantly, and this creates an abrasion on the rigging that is very cyclic and in one concentrated location. It takes more time, but when sailing long distances on the same points of sail especially, this too can lead to damage.’
‘In the first phase of the research we were looking mostly at high-speed chafe’ says de la Cuesta. ‘For testing, we started with the DNV standard for carbon rigging, which we normally do to certify our products. But soon we realised this protocol didn’t go far enough – basically, test results didn’t show any real problems even though we knew that real-life situations could lead to them. We had to redesign the test protocol.
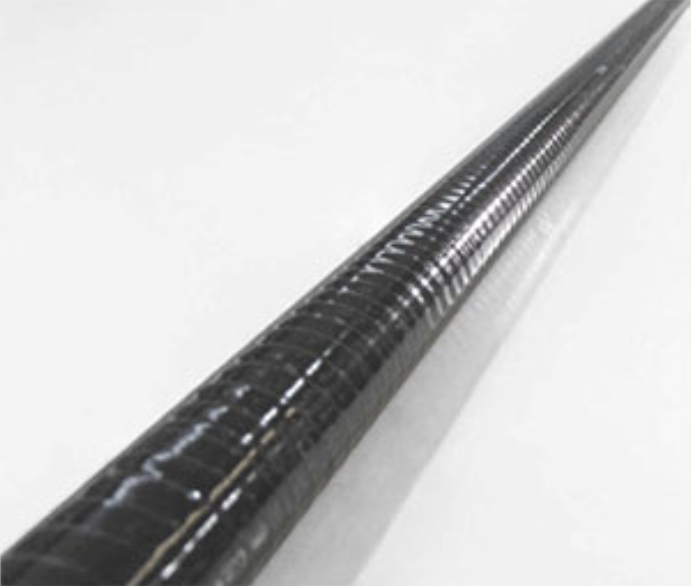
‘To design a better test setup, we consulted our colleagues at RigPro to pool our collective handson experience regarding the variety of lines’ materials, diameters, and speeds in use today in the Grand Prix circuit. This gave us a range of parameters with which to perform an initial parametric study, but also provided the boundaries for the newly designed test apparatus. We basically came up with a system where we used closed loops to simulate the actual running lines. The device was straightforward: a loop running around two pulleys, driven by an electrical motor and with a sample of our standing rigging positioned inside. The setup allowed us to test different line tension, angle, speed, and event duration and of course try out any rope or stay material.
‘The parametric study assessed the effect of each of these variables on the chafe damage characteristics and involved runs of up to 30s duration and 4m/s line speed, line angles in the range of 10º to 45º, and line loads of hundreds of kilos. Different line covers like Polyester, Technora, Zylon ChafeShield or Dyneema were included in the programme. The new setup allowed us to achieve the sort of damage that can take place in real situations. A set of parameters was then selected within the boundaries of those variables aiming for a realistic configuration which would provide measurable damage yet enough resolution to quantify new materials’ improvements. With this test configuration we ran through all our test samples. We used a thermal imagining camera to monitor the surface temperature of the tested materials and measured the removed material to rank the chafe resistance of the different solutions.’
‘We tested and developed a solution applicable to two of Future Fibres’ carbon rigging technologies, multi-strand ecsix and razr solid rigging,’ says de la Cuesta. ‘We tested various coatings, fibres, cure temperatures, tried out different mixes of materials, additives and so on. The use of composite materials guaranteed the compatibility and integrations with the cables’ structure while allowing for material tunability and ensuring the lowest weight and thicknesses possible. ChafeShield, the resulting cover product, is built from an advanced fibre that came through our testing as the best. For the matrix, it was not enough to work only with basic “temperature resistant” systems, and we had to dig deep into the chemical properties of the resin, including collaboration with resin formulators who developed a bespoke system especially suited to our requirements.’
What came out of this was a rigging solution with significantly better ability to withstand high speed chafe’, says de la Cuesta. “The final ChafeShield composite cover is designed for multi-strand and solid fibre rigging and reduces chafe depth on carbon stays up to nine times compared with legacy materials. The protective layer is only 0.5mm thick and very light compared to other solutions in the industry, so the effect on weight and windage is minimal. Application areas can be tailored to individual projects allowing for optimised performance. ChafeShield becomes an integral part of the shroud but can still be retro-fitted on existing stays in many cases.’
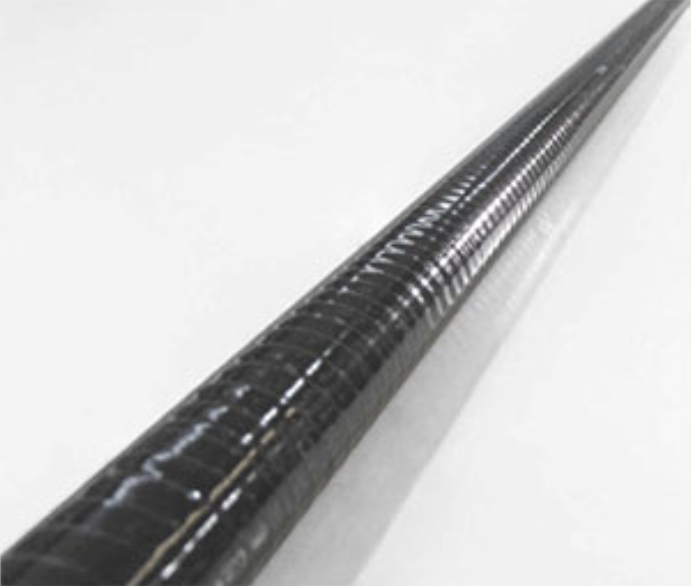
De la Cuesta continues: ‘Lowspeed chafe is fundamentally different from high-speed chafe. Again we had to create our own test setup. We designed a bench where a high-abrasive material under load dragged back-and-forth over the shroud. The test was far more aggressive than what happens in reality, to accelerate the process. In much the same way as with high-speed chafe, we used this setup to try out different materials under a standardised schedule and measure the results.’
‘Through our test programme we found that materials which performed well for high-speed chafe did not necessarily perform as well under low-speed chafe. So the material selection and the method of application had to be different. For low-speed chafe, self-lubricating low-friction materials proved to be the best option. The final design — found to be six times more resistant than existing solutions — joins Future Fibres’ Chafeguard range of clippedon chafe protectors, which now incorporates a tailored solution for areas highly exposed to cyclic abrasion. The Chafeguard is removable and easy to install and replace if worn out.’
The first ChafeShield implementation took place in summer 2023 on a TP52 razr project, with more TP52s added to the list this summer. The J Class Rainbow will be fitted an ecsix forestay with ChafeShield cover this season alongside other projects like V racing and Lucky.
‘These are products for boats that have or will have Future Fibres composite rigging and not necessarily only for professional racing boats’, says Cooley. ‘Many superyachts and large cruising vessels will benefit from these upgrades as well. More and more we see the lines being blurred between the superyacht and racing worlds with owners and crews anxious to push their maxis just as hard as TP52s and this is a great option for those clients. It is not just a question of safety and risk mitigation, but also about reducing running costs and extending rigging service life.’