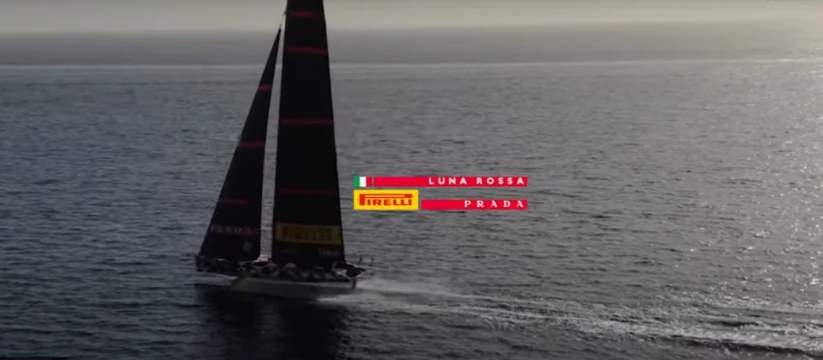
Inside the construction process
Vi raccontiamo come è stata costruita Luna Rossa
La laminazione del carbonio è una tecnica delicata e complessa. E non è da tutti, perché, per riuscire alla perfezione, richiede tempi precisi, esecuzione impeccabile e persone di grande esperienza. Come Julien Meunier, Construction Manager e Process Engineer, che ricopre il doppio ruolo di project manager e di link tra il design team e quello addetto alla costruzione.
«Il mio lavoro iniziale è sviluppare i database dei materiali, in modo che gli ingegneri che dovranno disegnare le strutture siano perfettamente a conoscenza di quelli che useremo per la costruzione», spiega. «Poi mi accerto che questi materiali corrispondano a quanto testato e, infine, fornisco ai costruttori le linee guida».
Da un lato, quindi, Meunier si assicura che il processo di costruzione avvenga alla perfezione e secondo i tempi prestabiliti e, dall’altro, si accerta che che la struttura in composito si comporti come da progetto. «Ogni singolo pezzo in carbonio – prodotto in casa o fornito da supplier – deve corrispondere esattamente alle specifiche progettuali ed essere consegnato nei tempi previsti, perché il ciclo costruttivo ha una tabella di marcia che non si può modificare, pena l’accavallamento di più dipartimenti».

Scafo e coperta nascono da stampo femmina (concavo) - per avere una finitura esterna praticamente perfetta che quindi necessita di una piccolissima quantità di filler (insieme di stucco e vernici di riempimento per uniformare la superficie), minimizzando il peso - e hanno una classica struttura a “sandwich”, costituita da un’anima strutturale (schiuma o corecell a nido d’ape, generalmente in alluminio) “inserita” tra vari strati di pelli di carbonio preimpregnato di resina epossidica. Il procedimento in sé non differisce da quelli riservati alle barche da regata più competitive: dopo aver steso un determinato numero di strati di carbonio, lo stampo viene messo sottovuoto per risucchiare le eccedenze di resina e infine “cucinato” in forni speciali affinché quest’ultima catalizzi perfettamente. Questo ciclo si ripete sino alla perfetta esecuzione e all’estrazione dello scafo dallo stampo.
Quello che fa la differenza tra Luna Rossa e una generica barca da regata, o un altro AC75 di Coppa, è nascosto nella formula “segreta” della ricetta: la tipologia del carbonio utilizzato, il materiale scelto per formare il “core” (decisi dagli strutturisti in fase di design) e la corretta applicazione da parte dei laminatori sono, infatti, “ingredienti” top secret. È anche molto importante rispettare i tempi di esecuzione tra un passaggio e l’altro, assicurandosi però, di essere veloci per lavorare la resina fresca.
«Se la laminazione non è fatta a regola d’arte», spiega Meunier, «non solo si rischia la delaminazione, ma soprattutto è quasi certo che la barca non performerà a dovere. Basta una fibra non orientata bene perché si senta la differenza in navigazione e i velisti se ne accorgono subito».
Tutte le parti - con particolare attenzione ai punti di attacco, che sono rinforzati (stralli, running rigging, appendici…) - vengono singolarmente testate prima e dopo la costruzione e la stessa cosa si farà con lo scafo finito. Se questo non bastasse, il Quality Control Manager, Stefano Beltrando, esegue durante l’intero processo test CND (controlli non distruttivi) per monitorare e segnalare eventuali anomalie, anche minime.
Una volta estratto dallo stampo e rifinito in ogni sua parte, lo scafo deve essere verniciato. Con la sua grafica innovativa e di grande impatto visivo, il prototipo Luna Rossa ha catturato a lungo l’attenzione del pubblico e i riflettori della stampa. Non tutti sanno, però, che quella complessa livrea geometrica è stata fatta interamente a mano. In che modo, ce lo racconta Mauro Zamichele che, insieme a Valentino Melis e Danilo Sorrentino, lavora nel dipartimento verniciatura di Luna Rossa Prada Pirelli e ha realizzato questo piccolo capolavoro. «Una volta terminata la fase di laminazione», spiega Zamichele, che fa anche parte del team R&D, «abbiamo preparato lo scafo dando una mano di primer (base) bianco di alta qualità; poi abbiamo tracciato con il laser le linee guida e le varie bande per i nomi Luna Rossa e Prada e quindi ci siamo dedicati alla grafica».

E qui viene il bello, perché bisognava riprodurre un disegno 2D – molto complesso – su una superficie 3D. «A quel punto ci siamo resi conto che le proporzioni non sarebbero state rispettate e che l’unica opzione valida era fare il lavoro interamente a mano», prosegue. Ovviamente sono state usate delle mascherature, ma le varie modifiche andavano fatte singolarmente e manualmente, soprattutto per rispettare la simmetria tra la parte destra e quella sinistra dello scafo. «Una volta capito che i triangoli avevano un senso logico il lavoro è diventato più semplice e alla fine è stato davvero gratificante vedere lo scafo finito; è stato un lavoro di squadra e Danilo e Valentino sono stati bravissimi». A quel punto, sulla livrea è stata stesa un’altra vernice «molto particolare e altamente tecnologica riservata a imbarcazioni che devono essere “leggere” e che non restano a lungo in acqua, ma che, dall’altro lato, hanno bisogno di una finitura perfetta. Stenderla non è semplice perché siamo a un punto dell’esecuzione in cui diventa difficile correggere eventuali errori».
Sulle imbarcazioni di Coppa America, dove ogni cosa è estremizzata in funzione delle prestazioni, anche la vernice ha un ruolo cruciale. Per questo, al termine di ogni sessione in mare, Mauro e Valentino controllano tutto lo scafo, concentrandosi sulle appendici (verniciate con un altro prodotto ancora), per verificare che non ci sia neanche la minima imperfezione: bastano un graffio o una bolla, infatti, per creare delle turbolenze che possono influenzare la velocità e la qualità del “volo”. La fase di verniciatura è durata circa 10 giorni e ha seguito un calendario ben preciso: «ll reparto di verniciatura ha lavorato di notte alternandosi con i tecnici di altri dipartimenti per non intralciarci e, contemporaneamente, rispettare le scadenze», conclude Zamichele.
Tra questi tecnici ci sono Marco Donati e Massimiliano Carbone, responsabili, rispettivamente, dei reparti di elettronica e idraulica. Il primo, che lavora con Davide Cannata e James Sweetman, ci spiega l’importanza del suo settore: «L’elettronica è il cuore della barca», dice; «per come sono concepiti, i nuovi Coppa America senza batterie non si muovono. Fondamentalmente ci occupiamo di tutto l’hardware, del cablaggio, della customizzazione dei prodotti, dei sistemi di comunicazioni e di altre applicazioni, sia per la barca da regata, sia per quelle appoggio».

Moltissima parte di questi sistemi viene prodotta in house, oppure customizzata dal team. «Costruiamo tutto quello che possiamo, per avere il controllo del pezzo sin dalla fase di progetto», prosegue, «e quello che acquistiamo viene comunque personalizzato per combaciare con le nostre esigenze e per essere perfettamente stagno». I pezzi industriali, infatti, non nascono per essere utilizzati in mare a 50 nodi, mentre per il team bisogna che funzionino perfettamente in condizioni estreme. Così vengono resi impermeabili o racchiusi dentro scatole totalmente waterproof disegnate e costruite internamente. «Dei sistemi di bordo l’80% è custom», dice Donati. «Dal momento che il prototipo nasce per testare tutta una serie di soluzioni, paradossalmente è molto più ingombro di sistemi, cavi e device di controllo dell’AC75, perché dobbiamo imparare a conoscerli e vedere come interagiscono tra loro prima di decidere quali traslare sulla barca ufficiale. Fondamentali sono le batterie, dato che attiveranno i sistemi idraulici che movimentano i foil. Anche qui è necessario attingere all’ultima tecnologia disponibile e provvedere a personalizzarla, sia per renderla impermeabile sia per fare in modo che pesi il meno possibile».
Se in assenza di batterie le barche sono ferme, senza idraulica addio movimentazioni e foil… Su un AC75, infatti, i sistemi idraulici sono vitali, come spiega Massimiliano Carbone, responsabile di questo reparto, dove lavora insieme a Davide Pescuma.
«Per idraulica si intende tutto quello che è applicato con una forza oleodinamica», spiega; «al posto di una forza meccanica applicata alle varie utenze della barca (cime ecc), infatti, c’è adesso una pressione dell’olio che va dentro a degli attuatori lineari chiamati cilindri, che a loro volta la smistano alle varie utenze che movimentano le funzionalità della barca». A bordo dell’AC75 ci sono tre circuiti (chiusi e separati): quello che fa muovere gli arm (Foil Cant System) che è one design e quindi uguale per tutti; quello che fa muovere il sistema di volo (Foil Flap System) che determina con flap e timone l’altezza di volo e quello che movimenta le vele (Sail System). Questi ultimi due sono “liberi” e quindi disegnati e sviluppati dal team.
I tecnici dedicati all’elettronica e all’idraulica effettuano controlli continui sulla barca: prima della messa in acqua, durante gli allenamenti e le regate (dalle barche appoggio tramite i monitor) e al rientro in banchina, per far sì che tutti i sistemi siano regolati come da programma e che funzionino correttamente.
