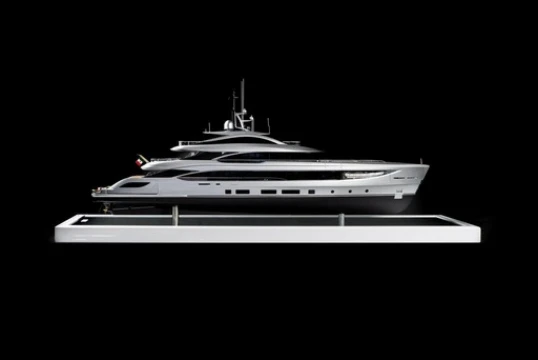
Model Maker Group, the international success of the best-known yacht model manufacturer
Model Maker Group: new frontiers for the scale yacht atelier
For those visiting boat shows, whether they are boat owners in search of their next vessel or industry professionals, with journalists at the forefront, it has become customary to find scale models at various stands not only of the boats on display but also of the new designs that shipyards announce for upcoming seasons. These models are highly effective marketing tools, and their use has become indispensable for every brand because they provide a physical and tangible representation of the project, allowing potential buyers and investors to visualize the design and size of the yacht in a more concrete way, offering an even truer, more realistic perception compared to drawings or digital images.
Scale models can showcase details and finishes with high precision, allowing an appreciation of the quality of the design and the care taken in the interiors and exteriors, which are key aspects in the construction of luxury yachts.
Model Maker Group, in the realm of scale yacht models, is undoubtedly a point of reference for all brands offering luxury boats and yachts. Giuseppe Capobianco, the passionate model maker who created the company and then succeeded, together with his wife Elisabetta Fantasia, CEO of MMG, in transforming it into a hi-tech factory capable of providing yacht models to many of the most important national and international shipyards, is today one of the most well-known individuals in the yacht industry. The quality produced by his company, the incredibly faithful details replicated on his models, and also his availability, always ready to take on new challenges and to maintain complete confidentiality on new projects in which MMG is involved, have made him a reference point for much of the sector.
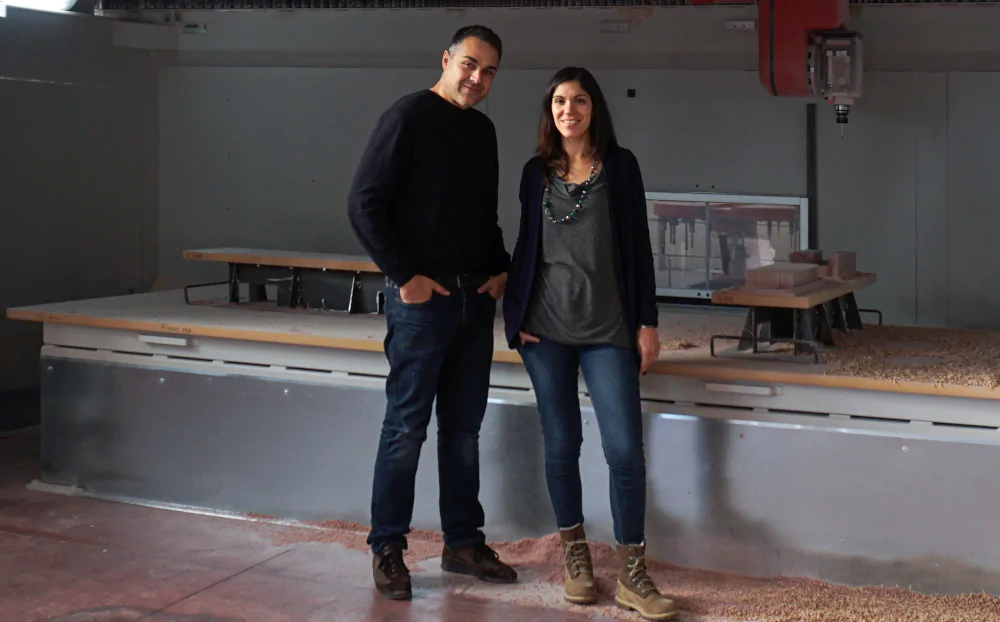
We interviewed Giuseppe Capobianco during a visit to the MMG production facilities, a true atelier for shipyards and architects, where we discovered that the company, in addition to scale yachts, now produces components for actual yachts.
PressMare - Giuseppe Capobianco, can you explain how this new sideline for MMG came about?
Giuseppe Capobianco - Over the years, we have enriched our personal technical knowledge, mine and that of the whole team working with me, but above all, we have invested many resources in implementing the technology necessary to build scale models that are increasingly realistic in terms of yacht design and detailing of each aspect of the fitting, but also larger. We bought a first five-axis milling machine and then a second one, creating a dedicated division and equipping it with its own facilities. Then came the opportunity, a specific need from a shipyard that, knowing the quality of our work, asked us if we could supply a specific part of a yacht they were building. From there, we started working with the mills also on 1:1 scale pieces, and today we supply components for both nautical and industrial design.
PM - What kind of work do you do specifically?
GC - We do solid machining, so we can make whole pieces of great solidity, which don't need any gluing or puttying, like ventilation grilles, and they come out perfect with micron tolerances. With the milling machines, we are also working on carbon and ceramic processing to make molds used in foundries. Right now, we have several grilles, different parts to make for a 20-meter, for a 52-meter... It's a growing activity, but the core business of the company remains the making of models, the mills are mainly engaged in creating their hulls and superstructures of yachts, to meet the demand both from design studios and shipyards, which has certainly grown in recent years.
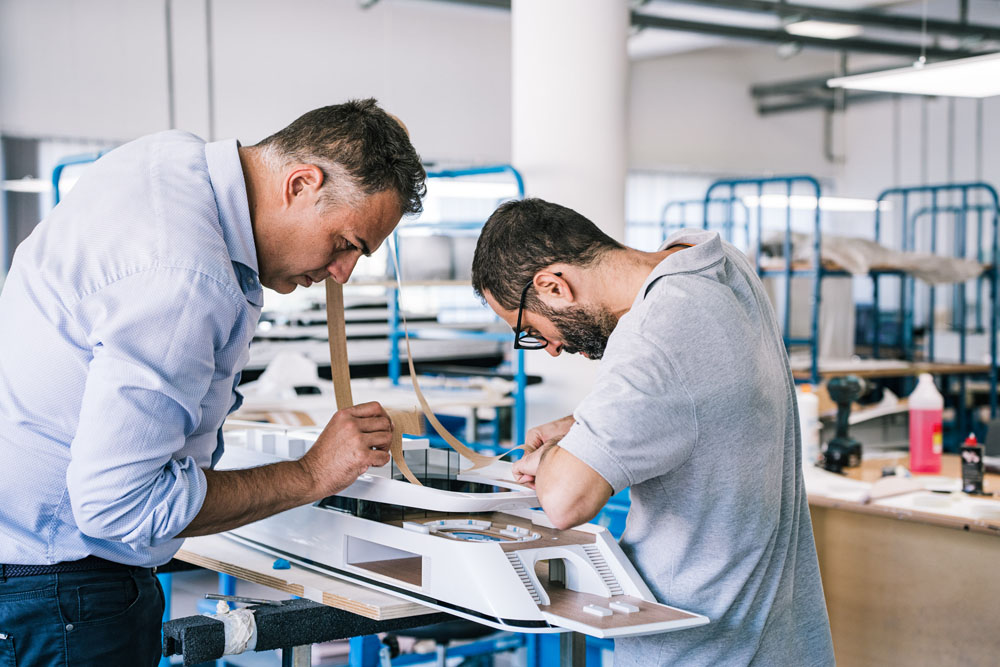
PM - So it's an advantage in terms of the quality of the finished product, the time it takes to make it, and also precision for the shipyards?
GC - Not even the shipyards knew, on an 80-meter boat, for example, sometimes you need "a piece" of a certain type and it doesn't make sense to make the mold which in these terms is more expensive than the piece required. For instance, sometimes grilles are needed, these are increasingly particular details, maybe with a custom design for that boat and so it doesn't make sense to make the mold. In the past for these purposes, we had seen 3D printing solutions proposed but then on that object, there was still a lot of manual labor left. Instead, we interpreted that request with milling for the production of that particular grille and the finished product could not be distinguished from the injection-molded one and was then selected instead of the other process. With the 3D printer, if you have to make very large objects you have to use very large nozzles which also means losing the various details, for example, on very small decorations, so you still need the craftsman able to then recover those details increasing consequently also the times of realization and delivery. In this case, therefore, it is still preferable to choose.
©PressMare - All rights reserved