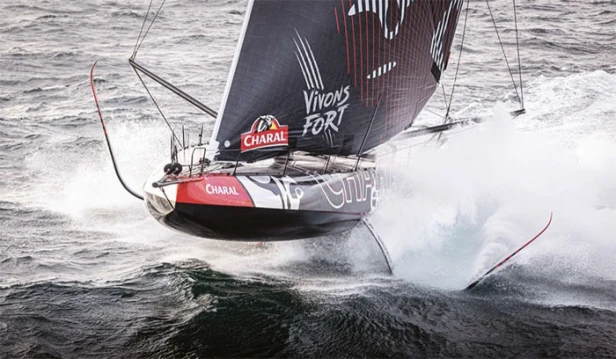
Most of the top Imoca 60s use Diverse Loadsense technology to monitor, log and optimise rig, foil and other loads onboard.
The accuracy of Diverse load sensors is almost taken for granted
The accuracy of Diverse load sensors is almost taken for granted by today’s serious racers but they just keep on getting better...
Yacht racing was, in general, slower to adopt load cell and data logging technologies than other disciplines. However, that’s not universally true. Diverse Performance Systems, for instance, introduced its Loadsense range more than 40 years ago.
Early clients included Lawrie Smith’s 81ft maxi Rothmans, which was built for the 1989-90 Whitbread. In order to identify the rig’s actual working loads she was fitted with an array of 29 load cells for a six week period of sea trials ahead of the race.
Similarly, Bill Koch’s 85ft Matador, winner of the 1990 Maxi World Championship, used 14 Diverse Loadsense monitors to optimise the rig design and settings. These were interfaced with an onboard computer to display, log and print rig and hull loadings, linking them to wind speed and angle, boatspeed, heel angle and so on. Just two years later Koch’s America³ team went on to win the America’s Cup, with Diverse founder Lou Varney on board.
The firm’s client list now reads like a Who’s Who of the top of the yacht racing world, including seven of the top 10 Imoca 60s (and all the top three boats), TP52s including Gladiator, Allegra and Quantum, plus several Wally yachts and Gunboat cats. Loadsense is also used across the ClubSwan 50, Cape 31 and RC44 fleets.
Today the company produces load cells for a very wide range of raceboats and superyachts from less than 30ft to 300ft. The portfolio of products stretches from a maximum working load of one tonne right up to 250 tonnes and pin diameters from 8mm to a truly massive 150mm. Some of these have now been providing reliable service in the field for more than 20 years, with the only maintenance required being occasional calibration.
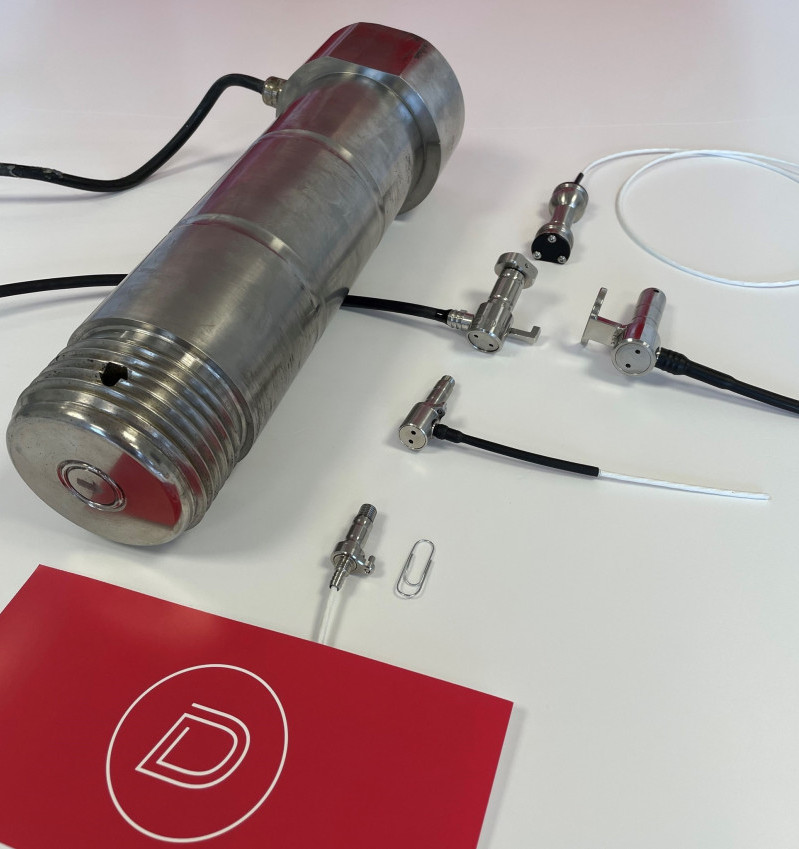
‘It makes sense to put a load cell anywhere that a pin is used,’ say the Loadsense team, ‘as the additional weight of cabling and amplifiers is minimal, but the data captured can be invaluable.’ Pins are available for use in all rigging positions and hydraulic systems. If necessary fully custom products can be produced to meet the exact requirements of a specific application.
In addition, the Loadsense range includes aluminium, stainless steel and titanium shim sensors with maximum working loads from four tonnes to a massive 600 tonnes. These are used to monitor mast foot compression and in foil systems.
In many domains we have become accustomed to the apparent simplicity of wireless data transfer. However, when measuring dynamic loads there’s a strong case for wired sensors with a high-speed data output that doesn’t need to be throttled back to maintain battery life.
Wired load pins offer reliable information that isn’t susceptible to either signal interference from carbon construction, carbon sails and so on, or from battery life constraints. This means real time load data is seen and recorded, with fast data rates that suit the most meticulous data analysts.
Diverse worked with the major marine electronics suppliers to bring the N2K output option to market, with system integration for all major sailing processors, as well as stand-alone display options. The Diverse range now includes 0-5V, 4-20mA, N2K and CAN output options, many of which can be integrated into the pin itself if required. Equally, various cable and connector specifications are available to best suit different installations. In addition, wireless transmitters allow integration with iOS and Android devices.
In the early days of load sensing, the majority of pins were made to replace the supplied pins in standard rigging interfaces. By contrast, today the majority are specified at an early stage during the design processes. This allows for innovative securing and anti-rotation methods to be specified and to optimise cable routing, as well as giving an opportunity to incorporate more complex products such as those for composite chainplate bushings.
More than 40 years of experience in an evolving market gives Diverse Performance Systems the ability to supply the basics and equally to innovate to suit the most demanding custom requirements of both grand prix raceboats and the world’s largest superyachts.
With thousands of pins, shims and links supplied over the years, with diameters ranging from 8mm up to over 150mm, along with mast shims for loads in excess of 600 tonnes, the company has unparalleled ability to supply products that will suit the requirements of any boat.